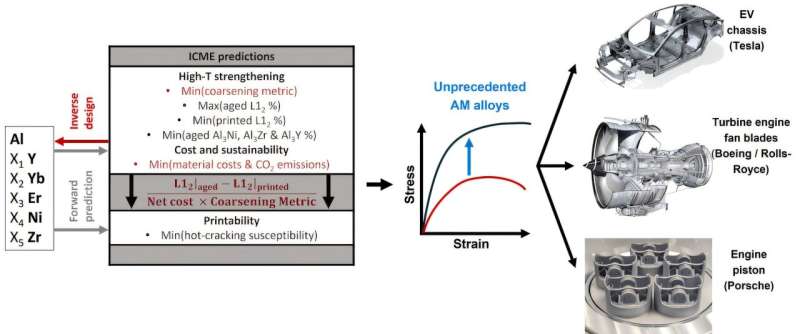
Could reshape automotive manufacturing by combining high strength with lower production costs using advanced 3D printing techniques.

A study from Carnegie Mellon University (CMU) and the Massachusetts Institute of Technology (MIT) has introduced a novel printable aluminum alloy system that promises to transform the automotive industry by balancing high strength with reduced costs. Aluminum alloys are widely favored in automotive and aerospace sectors for their strength-to-weight ratio and affordability. However, their performance at high temperatures — critical for components like engine pistons and jet engine fan blades — is limited. Most conventional aluminum alloys lose strength at elevated temperatures and lack cost-effective, sustainable design strategies.
In contrast, alternatives like titanium alloys, although effective, are nearly twice as expensive and more difficult to machine. To address these challenges, CMU and MIT researchers leveraged computational simulations and optimization algorithms to design aluminum alloys compatible with additive manufacturing (AM). Their work introduces a new alloy family based on aluminum, nickel, erbium, zirconium, and yttrium (Al-Ni-Er-Zr-Y). This system offers up to 95% of the strength of benchmark printable aluminum alloys while delivering a projected 15% cost reduction. A second formulation optimized for room temperature use achieves equivalent strength at just 20% of the benchmark cost.
The team employed a high-throughput Integrated Computational Materials Engineering (ICME) framework based on CALPHAD modeling, coupled with machine learning, to analyze composition-process–structure–property relationships. Laser-based AM methods, which enable rapid solidification, were instrumental in forming unique microstructures that enhance the material’s strength by exploiting metastable phases that only form under these fast cooling conditions.
“This development could significantly impact the automotive sector, where there’s high demand for materials that combine performance, sustainability, and cost-efficiency,” said Assistant Professor Mohadeseh Taheri-Mousavi of CMU, who co-led the study with Ph.D. student Benjamin Glaser. This research opens the door to next-generation lightweight, printable aluminum alloys tailored for high-demand industrial applications with a strong emphasis on sustainability and cost-effectiveness.