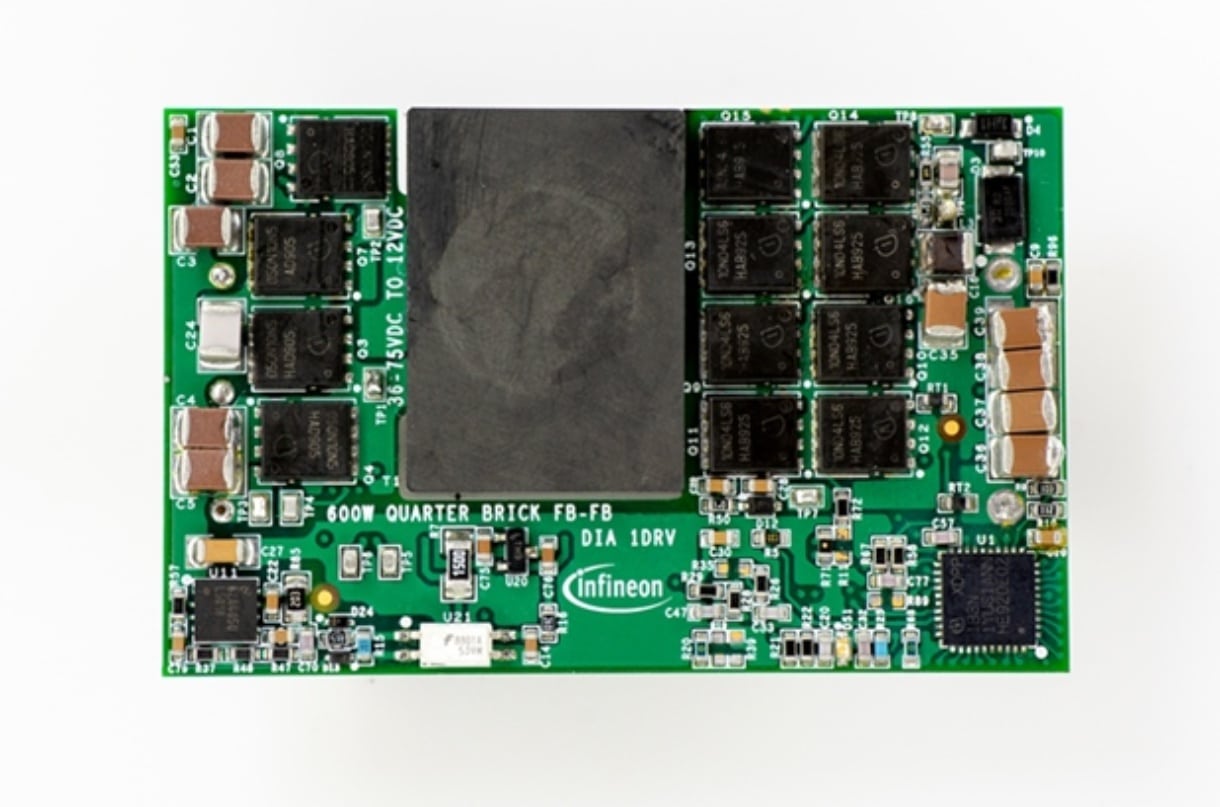
The 600 W full-bridge power supply design with digital control, fast response, and PMBus support for telecom, server, and industrial power systems.

The REF_600W_FBFB_XDPP1100 is a telecom-focused isolated DC-DC power module system solution that delivers up to 96% peak efficiency within DOSA-standard quarter brick form factors. The reference design from Infeneon features a secondary-side digital control and a hard-switching full-bridge topology, providing 12 V at 600 W output power. Potential applications include isolated DC-DC brick modules, telecom infrastructure, server motherboards, 48 V computing and datacenter SMPS (switched-mode power supplies), as well as Industrial 4.0 environments.
The design supports a wide input voltage range from 36 V to 72 V. Achieving a power density of 22 W/cm³, this high performance is made possible by the integration of the XDPP1100 digital controller, OptiMOS MOSFETs, and the EiceDRIVER gate driver IC.
The digital controller offers exceptional integration and performance in a single-chip package. It combines an optimized analog front end, multiple pre-programmed peripherals, a fast state-machine control loop, and an embedded microcontroller. This innovative architecture enhances isolated DC-DC converter performance, reduces bill of materials (BOM), and enables advanced control features and customization—accelerating time to market.
This reference design leverages key components including the OptiMOS 5 100 V, OptiMOS 6 40 V, and the EiceDRIVER 2EDF7275K dual-channel isolated gate driver IC. The 2EDF7275K provides high drive current, excellent common-mode noise rejection, and fast signal propagation, making it ideal for driving medium- to high-voltage MOSFETs in fast-switching power applications.
This design is a digitally controlled isolated brick converter that utilizes voltage mode control with built-in flux balancing and transformer flux walking protection. It delivers a fast response to both line and load transients, ensuring stable and efficient operation under varying conditions. Communication is enabled through PMBus and I2C interfaces, allowing seamless integration into digital systems.
The converter offers best-in-class feed-forward response and supports active current sharing across multiple modules, improving system scalability and performance. It features a smoother pre-bias start-up, reducing the risk of disruptions during power-on sequences. Additionally, it ensures output voltage accuracy within ±1% across the full operating temperature range of -40°C to 125°C, making it reliable for use in harsh environments.
The converter is highly configurable via a graphical user interface (GUI), enabling firmware-based customization to meet specific application needs. Its digital control architecture enhances overall system reliability and allows for configurable output voltage, offering flexibility in design. By integrating key components, the converter achieves high power density and a reduced bill of materials (BOM), which helps lower system costs.
With pre-programmed control features, the design supports the fastest time-to-market for new designs. Furthermore, it provides a future-proof solution through PMBus-enabled adjustments, ensuring adaptability for evolving application requirements.
Infineon has tested this reference design. It comes with a bill of materials (BOM), schematics, assembly drawing, printed circuit board (PCB) layout, and more. The company’s website has additional data about the reference design. To read more about this reference design, click here.